作者 | 胖腿,科研工作者
渣油,又称为“桶底油”,是石油中最难以利用的重质组分,不但硫含量极高(2~4%以上),金属含量更是高达200ppm以上(主要为镍和钒)。渣油通常只能作为沥青或炼制焦炭使用,经济价值极低,因而往往是石油工业的鸡肋。
为了降低石油炼制过程的污染,提高炼油利润,将渣油加氢转化为汽柴油等经济油品是最佳的生产路线。中国经过数十年的研发,终于突破国外技术垄断,开辟全新的技术路线,利用专利技术反应器和催化剂实现了渣油自循环沸腾床加氢技术,使低成本渣油清洁转化成为了可能。
(一)石油被精炼后,剩下的就是桶底油
目前世界能源的核心“硬通货”仍然是石油资源,占据了世界能源消耗的33%以上。根据BP公司(British Petroleum,英国石油公司)在2017年报告中的分析数据,目前世界探明石油储量已连续多年上涨,相比20年前增长了1.5倍之多(达到1.7×1012桶),彻底宣告了石油峰值理论的破产。
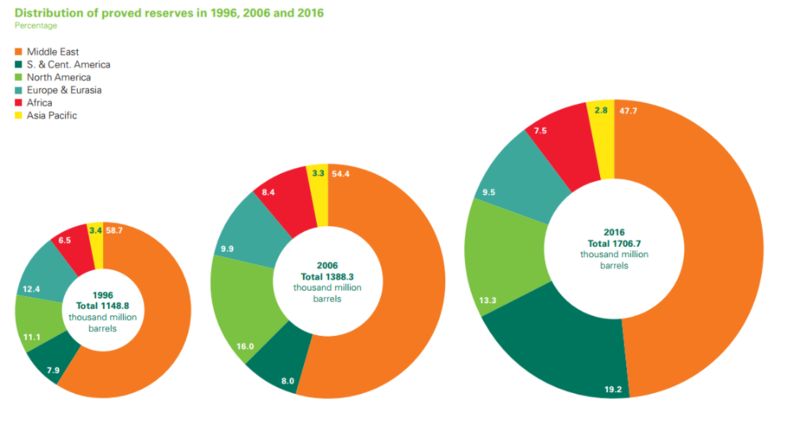
▲世界石油探明储量逐年上升,委内瑞拉更是快速占据了世界石油储量第一的位置
石油被称为黑色黄金,其价值不言而喻,从中分离得到的各种组分的产品更是人类整个工业体系的核心。从天然气到汽柴油,从汽车轮胎到LEGO玩具塑料,无不是由石油及其制品获得。因此,充分利用石油中的每个组分,是符合当下社会环保、节约理念的最佳生产方式。
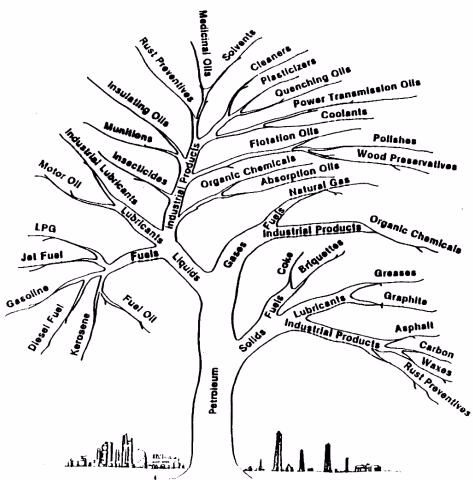
▲石油及其衍生制品
石油被开采出之后,必须经过精炼才可以被利用,以满足不同用途的特殊要求。通过沸程的差异可以将石油划分为石脑油、汽柴油、航空煤油、重质蜡油和减压渣油等组分;通过进一步的重整、加氢精制、催化裂化、加氢裂化、烷基化等单元装置的处理,这些馏分油被精炼成了我们熟知的聚乙烯、塑料、汽油、柴油、煤油、润滑油等产品。
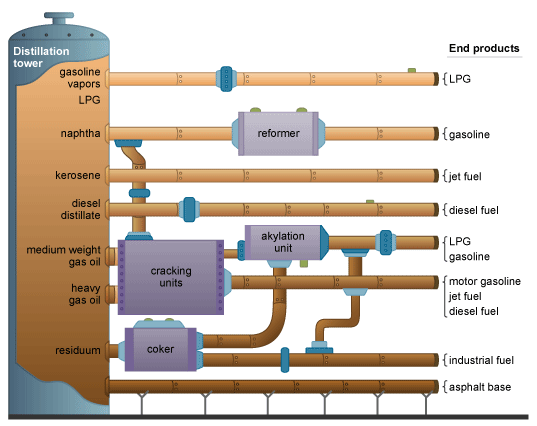
▲炼油厂中的石油炼制关键装置和对应产品
当所有轻组分都被榨干后,留下来的就是最难处理利用的“减压渣油”,又被称为沥青或“桶底油”。渣油的性质极差,不但碳含量高,性质粘稠,其中也富集了石油中90%以上的硫、氮、镍、钒等元素,可以说几乎没有利用价值。
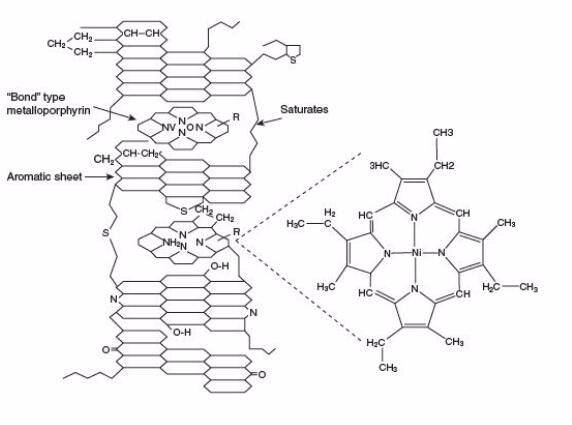
▲渣油、沥青的分子结构示意
▲沥青滴落实验,除了铺路以外,以前的渣油似乎也只能来生产段子了
炼油厂中普遍采用焦化(Coker)对渣油进行处理,通过富集碳原子,让渣油变成焦炭,同时将部分渣油转化为轻质的汽柴油和液化石油气,使又脏又稠的渣油得到了一定程度的利用。
然而,随着环保问题的日益严峻,中国已经颁布了最新的沥青、石油焦、船用燃料油标准,其中严格限制了这几种产品中的硫和金属含量。焦化过程的原理决定了其生产过程不能脱除任何杂质,因而其生产的石油焦都是不满足市场规范的,完全无法销售。
在越来越严格的环保要求和油价剧烈波动的市场环境下,炼油厂面临着两难的境地,如果不处理渣油,那么将减少一大块的汽柴油产出;如果处理渣油,不但产出的沥青、石油焦无法销售,甚至都不能用于船用燃料油。沙特的炼油厂就出现过用大面积的厂区囤积无法销售的高硫石油焦的情况,当沙尘暴袭来,焦炭粉末混着沙子飞向沙漠的场景实在是令人恐惧。
(二)桶底油 又脏又稠, 处理是个难题
对于油中的主要杂质元素,如硫、氮、金属等,最有效的方法就是通过加氢反应使杂质与氢原子结合而被脱除。
加氢过程的核心在于利用氢气的反应活性使有机物中的硫、氮等生成硫化氢、氨气,辅以高温下的大分子有机物热裂化,使金属等从有机物中析出,最后实现杂质的脱除。反应中同时存在着加氢裂化和热裂化过程,因此部分重质渣油会转化成轻质的石脑油、柴油等,在一定程度上提高产品价值。
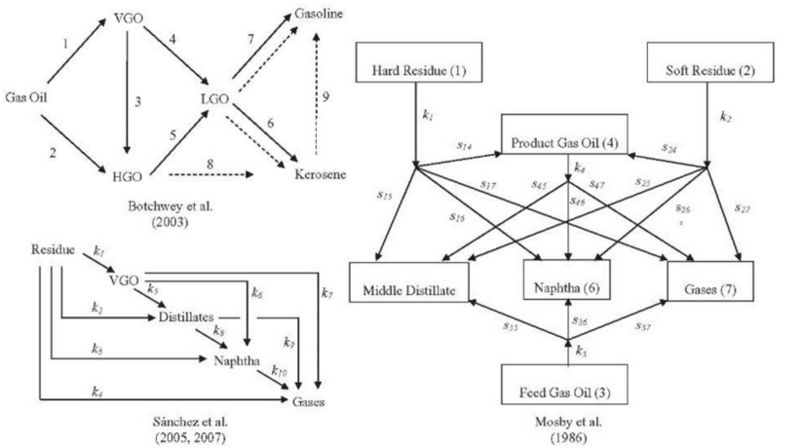
▲渣油加氢的反应路线
加氢工艺需要在高温高压下进行(60~150大气压,200~450℃),对于汽柴油、航空煤油等油品,只要将催化剂堆积在反应器内,让原料油与氢气一同流过反应器并与催化剂接触,就能实现加氢反应过程。这种催化剂堆积在反应器内不移动的形式,被称为“固定床”反应器。
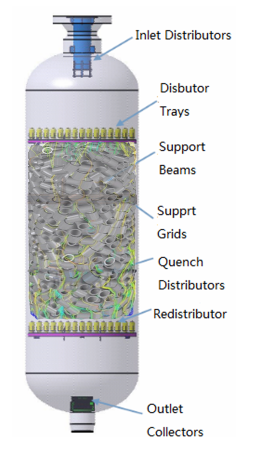
▲固定床加氢反应器,催化剂固定,而物料流过催化剂发生反应
可是这种简洁的反应器形式,在渣油面前显得脆弱无力。举例来说,想要让原料进入反应器,至少要保证原料的流动性。然而沥青十分粘稠,如果进入到反应器内,很容易把催化剂的缝隙堵住,最终导致完全无法流动。那把温度提高到200℃以上呢?这样确实可以让沥青软化,变为易流动的状态,然而温度提高会造成沥青缩合,最终变为焦炭,仍然会把反应器堵住。
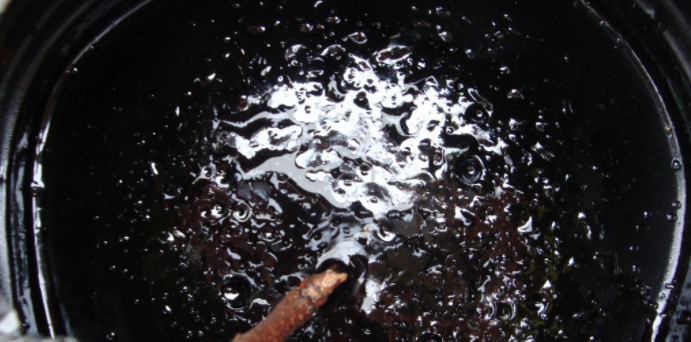
▲渣油
所以,固定床反应器想要应对渣油加氢工艺,要么选择加入蜡油、柴油稀释,要么频繁停工更换催化剂,利润非常低。当然,我们也可以准备多个反应器,随时进行切换保证连续运转,一个反应器堵塞了马上换到另一个反应器。但是,这种方法工程限制较多,仅切换管路的切断阀就需要耐住150大气压的压力差和400℃的高温,光这样的一个阀门的价格就可以高达6000万人民币。
(三)沸腾床工艺让桶底油变废为宝
从上面的介绍中可以看出,催化剂固定不动是固定床反应器的症结所在。机智的石油工程师想到让催化剂动起来,也就是所谓的流化床反应器。
20世纪50年代开始,美国就研发了应用于渣油加氢过程的流化床反应器。由于加氢反应过程需要通入大量的氢气,在反应器内形成大量气泡,这个过程非常像烧开水的沸腾状态,因此将这种反应器起名为沸腾床反应器。
经过多年发展和完善,目前渣油沸腾床加氢工艺形成了两家寡头垄断的市场,分别为法国石油研究院Axens公司的H-Oil工艺和美国谢夫隆-鲁姆斯国际合资的CLG公司的LC-Fining工艺。这两家的工艺可谓同源同宗,几乎没有差异,都采用0.8~0.9mm的条形催化剂,通过循环泵抽出反应器内的液体并打回反应器内,实现内部流动的提速。
通过完全移动的催化剂,完美解决了处理重质渣油、沥青过程中的各种限制,让渣油转化过程做到了高效、连续,即使在油价持续低迷的今天,也可保证渣油加氢处理过程获得极高的利润率。
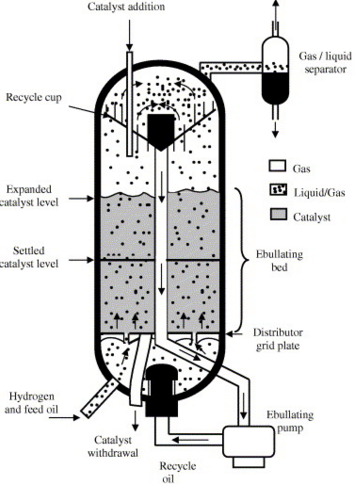
▲国外沸腾床渣油加氢技术反应器原理
这项技术应用60余年来,Axens公司和CLG公司已累计设计了38套沸腾床装置,且装置处理量越来越大,工艺越来越复杂,渣油转化越来越深。最新在建的炼油厂中,H-Oil渣油加氢技术的处理量甚至达到了530万吨/年,每年消耗催化剂将达到3000吨以上。
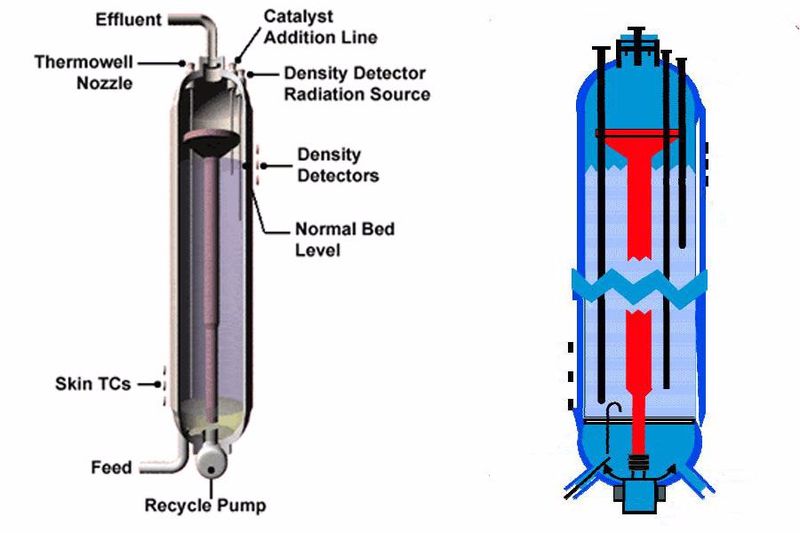
▲H-Oil工艺和LC-Fining工艺沸腾床反应器,除个别细节外,二者几乎没有差异
(四)国外长期垄断工艺,一台设备要花2个亿
如此完美的沸腾床技术也存在自身的阿喀琉斯之踵。
刚才提到过,高温高压极端工况下阀门的造价都已突破天际,而反应器中的循环泵也不是省油的灯。
这个循环泵不断将400度高温、150~180大气压的渣油和氢气抽出并增压返回,同时必须保证连续工作3年直到停工检修,中间不能有故障,而且还要保证生产过程的平稳进行。
要实现这样的性能,H-Oil和LC-Fining工艺中的循环泵满身都是黑科技,据说可能用到了航天发动机材料技术。要知道,航空发动机每运行几百小时后都要大修一次,而这台泵要保证全年8000小时全负荷运转,连续工作3~4年以上,直到炼油厂检修才能停工。
这样的泵自然是价格不菲,一台的单价高达2亿人民币。
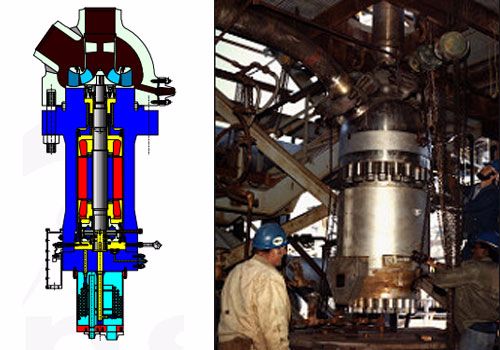
▲H-Oil工艺中的循环泵,简单结构的背后是满满黑科技的材料技术,其应用场景和专利工艺技术紧密结合,小众的应用市场使任何模仿技术或装置都面临巨大的研发成本压力
此外,这个循环泵还需要搭配一整套控制手段,才能保持在各种气液流速下,催化剂料面始终处于循环杯之下,既保证流化状态、又不会带出反应器。
循环泵的限制,加之国外技术的垄断和专利设备的漫天要价,让沸腾床渣油加氢工艺的成本居高不下。
(五)为了摆脱循环泵的困扰,中国从催化剂做文章
中国制造目前正处于发展的黄金时期,所有领域都争当第一,在渣油加氢领域也不例外。
中国每年加工近6亿吨石油,其中渣油含量达到了1.3~1.6亿吨。以70~80%的转化率计,这部分渣油至少能产出5000~8000万吨轻油,顶得上3~4个2000万吨大型炼油厂的年加工量!
既然是全新开发的技术,当然可以避免走许多的弯路。首当其冲的,就是如何去掉麻烦的循环泵。
从源头分析可以发现,循环泵的存在必要性是维持催化剂流化。那么如果让催化剂变得易于流化,是否可以免去循环泵的困扰?
沿着这个思路,中国开发出新型的球形催化剂,并降低催化剂直径,达到500μm,使催化剂的流化性能提高了4~8倍。通过优化催化剂生产过程,控制球形催化剂生产成本与条形相当,中国解决了催化剂对沸腾床反应器的限制。

▲中国沸腾床微球形催化剂
球形催化剂还有一个好处,就是易于离心分选。可以想见,排出的催化剂中肯定有部分仍然具有活性的催化剂,且密度与废催化剂不同。中国的沸腾床技术球形催化剂正好有利于催化剂的分离,通过密度差进行分选,从而有效利用废催化剂,进一步降低生产成本。
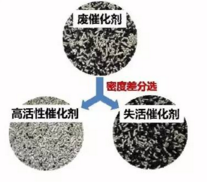
▲废催化剂的分选与回收再利用,高活性催化剂可以返回反应器,废催化剂可以进行金属回收或材料回收
去除循环泵后,反应器内的液体速度不足以维持催化剂流化状态。通过反应器内的结构设计,研究人员使反应器内流体形成内循环,利用渣油自身流动和氢气气泡浮力,带动了反应器内部流体的循环,使反应器液体速度大幅提升,催化剂跟随渣油一起循环,最终在无需外部动力加入的情况下使反应器自身达到完全流化的状态。
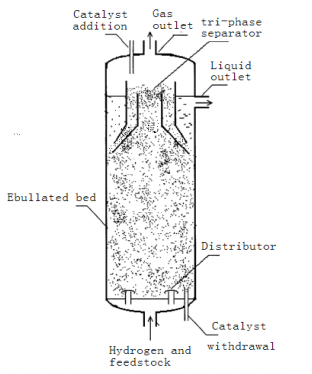
▲STRONG沸腾床专利反应器,通过内部结构设计使无循环泵的反应器实现了催化剂完全流化
结合催化剂形貌设计和反应器结构设计,催化剂得以充分流化,使反应器堵塞问题迎刃而解;由于球形催化剂接触更为充分,因而反应过程更为稳定可控,结焦风险也大幅降低。
然而,自由移动的微球催化剂也造成了催化剂夹带的难题。如何保证催化剂不被带出反应器是保证渣油加氢过程稳定工作的前提。通过设计特殊结构的三相分离器,中国科研人员将催化剂阻挡返回反应器,从而保证了反应过程正常进行。
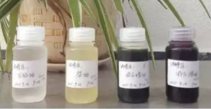
▲中国沸腾床技术对油品的转化(最右为原料渣油,左侧为转化的蜡油、柴油、石脑油等)
通过以上巧妙的设计,中国自主研发的沸腾床技术完全绕开了国外沸腾床技术必须使用循环泵的死穴,采用微球催化剂提升了催化剂流化性能,通过反应器结构改进促进了内部流体循环,设计三相分离器防止催化剂夹带、拓宽操作域,用简单、可靠的反应器实现了完全沸腾床渣油加氢过程。
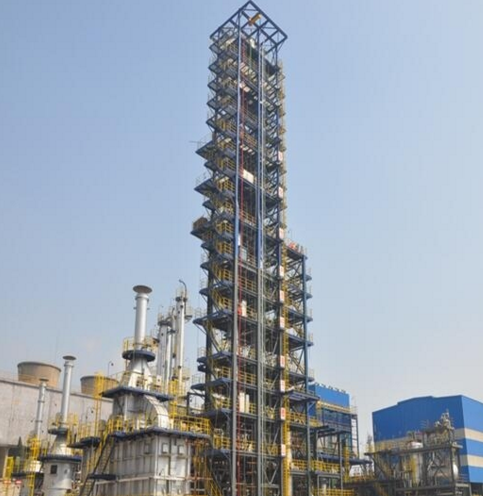
▲“STRONG”沸腾床装置
中国的这项技术取名为“STRONG”沸腾床,2016年,首套STRONG沸腾床示范装置开工,至今已完成了2000千余小时的连续运转。
与国外同类技术对比,中国的沸腾床技术单线反应可以达到80%渣油转化率;脱硫率、脱金属率等关键指标可以达到95%以上,等同或略好于国外同类技术。
结语
中国的石油炼制能力走在世界前沿,并逐渐甩开了欧美。与军工行业崛起不同的是,民用的化工领域受到专利制约,国外先进技术不但不能模仿学习,甚至不能出现应用重叠区域。
中国这次开辟的全新技术路线,无疑是国内炼油技术发展历程的一个标杆,这意味着中国也有能力开发出一套完全原创、自主研发的高科技技术。未来以中石化STRONG沸腾床技术为技术平台,国内多家炼油厂将充分利用重质油、渣油、沥青资源,实现渣油真正的变废为宝。
(文中图片均来源于网络)